- ALGER SIFTER
- BALL BEARING MILL
- BIG BAG FILLING FACILITY
- BIG BAG UNLOADING STATION
- CALCITE COATING PLANT
- CALCITE MICRONISING PLANT
- CONSTRUCTION CHEMICALS PLANT
- DOSING, WIEGHING, MIXING AND LIQUID MIXING UNITS
- DRYING SYSTEMS
- FLAPS AND FEEDERS
- HAMMER CRUSHER
- JET PULSE FILTER
- MICRONISED GRANULE PLANT
- PACKAGING AND WRAPPING
- PERLITE EXPANSION PLANT
- PLASTER PRODUCTION FACILITY
- RAYMOND
- SEPARATOR
- SILO AND SILO UNLOADING SYSTEMS
- SILO TOP FILTER
- VERTICAL AND HORIZONTAL CONVEYING SYSTEMS
- VIBRATING MILL
- VIBRO SIEVE
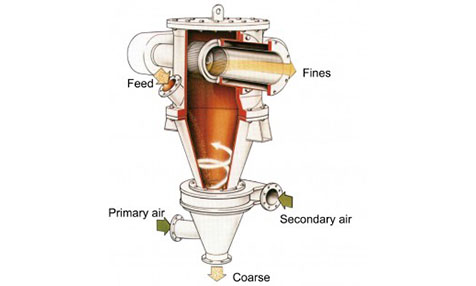
- DESCRIPTION
- TECHNICAL FEATURES
- PRODUCT VIDEOS
OPERATING PRINCIPLE
After entering the machine, classifier air flows in the centripetal direction through the classification rotor. In the process, classifying wheel extracts fine particles from feed material and transfers them to fine discharge cavity. Rough materials which are denied by classifying rotor are slope downwards. The air routing shown schematically is very simplified because before the coarse material exits the classifier, it is again rinsed with air to remove any remaining particles. This results in an extremely clean coarse fraction.
Product is either fed through a rotary valve or by an air flow classifier entering the classification air. Product fineness is controlled by adjusting the classifier wheel speed using a frequency converter. The horizontal operation of the classifying wheel means that even “difficult” products can be processed smoothly.
Air flow turbo classifiers, can be coated with ceramic. The body can be ceramic coated to prevent abrasive materials from damaging the machine body.
You can review the series in detail by clicking on the series below.
OPERATING PRINCIPLE
After entering the machine, classifier air flows in the centripetal direction through the classification rotor. In the process, classifying wheel extracts fine particles from feed material and transfers them to fine discharge cavity. Rough materials which are denied by classifying rotor are slope downwards. The air routing shown schematically is very simplified because before the coarse material exits the classifier, it is again rinsed with air to remove any remaining particles. This results in an extremely clean coarse fraction.
Product is either fed through a rotary valve or by an air flow classifier entering the classification air. Product fineness is controlled by adjusting the classifier wheel speed using a frequency converter. The horizontal operation of the classifying wheel means that even “difficult” products can be processed smoothly.
Air flow turbo classifiers, can be coated with ceramic. The body can be ceramic coated to prevent abrasive materials from damaging the machine body.
You can review the series in detail by clicking on the series below.
- ALGER SIFTER
- BALL BEARING MILL
- BIG BAG FILLING FACILITY
- BIG BAG UNLOADING STATION
- CALCITE COATING PLANT
- CALCITE MICRONISING PLANT
- CONSTRUCTION CHEMICALS PLANT
- DOSING, WIEGHING, MIXING AND LIQUID MIXING UNITS
- DRYING SYSTEMS
- FLAPS AND FEEDERS
- HAMMER CRUSHER
- JET PULSE FILTER
- MICRONISED GRANULE PLANT
- PACKAGING AND WRAPPING
- PERLITE EXPANSION PLANT
- PLASTER PRODUCTION FACILITY
- RAYMOND
- SEPARATOR
- SILO AND SILO UNLOADING SYSTEMS
- SILO TOP FILTER
- VERTICAL AND HORIZONTAL CONVEYING SYSTEMS
- VIBRATING MILL
- VIBRO SIEVE